Central impression cylinder is installed in Idyllic FP 6-1500
Idyllic FP press control panel with color touch-screen display
Powerful tunnel hot air dryer
|
Central Impression Drum Flexographic Printing PressesHigh productivity and outstanding quality, reliability and versatility at a reasonable price - these are the major requirements demanded of printing presses. Idyllic FP presses fully meet these criteria. Elaborate design and unique engineering solutions, which represent our own know-how, guarantee the highest quality output. Each machine part is designed to provide for maximum efficiency while remaining easy to handle.
Idyllic FP flexographic presses are designed for high quality printing on flexible packaging, i.e. plastic films (PP, OPP, LDPE, HDPE, PET, PVC), paper, aluminum foil, laminated materials, cardboard. Substrate thickness ranges from 7 micron. Idyllic FP presses are capable of printing complex high screen ruling jobs with excellent quality. Idyllic FP can work with alcohol-, water-based or UV-inks.
Idyllic FP presses include the following parts:
- printing unit (with a central impression cylinder and color stations positioned around it);
- unwind/rewind stations;
- connecting bridge;
- digital press control system.
Printing Unit
Side frames and the solid bottom frame of Idyllic FP presses are made of 80 mm heavy-duty structural steel mounted on the solid bottom frame. The chromed temperature-controlled double-wall central impression cylinder is mounted on precision-selected bearings. Idyllic uses central impression drums of German origin, manufactured by Drink&Schloessers Company - the main supplier of central impression drums for flexography in the world. The highest manufacturing quality at factories in Germany renders it possible to achieve minimal, up to 10 mcm, of total cylinder radial beat, to decrease surface roughness up to 23 mcm and to apply chrome protection coating, over 150 mcm, on a drum surface. The construction of the impression cylinder allows, in case of necessity, to demount it easily, without dismantling of the frame.
An AC servomotor of the main drive with the integrated reducer is placed in the bottom part of the frame underneath the impression cylinder.
Each color station has its own highly-efficient hot air dryer. A video inspection system is positioned immediately after the last printing unit, which makes it possible to monitor image registration fluctuation. The printing unit has protective covers with swinging doors made of robust and easy-to-wash composite material.
Color Station Design
The color station is equipped with highly-efficient chambered doctor blade systems. Doctor blade change is simple and does not require chamber disassembly. High-performance interstation hot-air dryers are installed after each printing station.
The color station locking system is used to provide for consistent print quality. Locking is done automatically when the machine achieves a given speed by means of two pneumatic cylinders locking the station in vertical and horizontal directions. The pneumatic cylinders can also be engaged manually from the control panel.
Each color station has a pneumatic diaphragm pump to supply ink to the doctor blade chamber of a unit. Pumps are installed on a standard ink tank by means of special cover.
During machine stoppage, color stations are automatically disengaged from the impression cylinder. Anilox rollers continue to rotate, driven by separate electric motors in order to prevent ink from drying. Plate and anilox cylinders are quick-detachable and are changed using electric hoists.
High stability of color alignment on Idyllic FP presses - is a guarantee of perfect printing quality.
All Idyllic presses feature original design of register adjustment system.
Additionally it is possible to install longitudinal and lateral register motorized system controlled via central panel. Longitudinal and lateral register adjustment range is ?10mm.
Precision of image alignment of the whole run on Idyllic FP presses is 0,1mm even with substantial alteration of printing speed during speeding and braking. It is provided by:
- original supporting of main gear of the CI-drum inside the frame, allowing to have short roller journals;
- thick solid walls mounted on heavy solid base;
- stiffness of structure and precision of mechanism operation;
- high precision of components manufacture and assembly of units;
- system of inking system secure fixation during printing mode;
- original construction of registration system, beating and skewing of bearings.
Unwind/Rewind Units
Just like a printing unit, the unwind/rewind unit of Idyllic FP presses has a robust structure with steel walls of 80 mm thickness, also mounted on a solid bottom-frame.
There are four supports with easily detachable pneumatic shafts mounted symmetrically on both sides of the frame, two at rewind and two at unwind. Support design makes it possible to equip the unit with automatic web guiding systems (both at unwind and rewind). To maintain constant web tension at the unwind, shafts are equipped with electromagnetic powder brakes. Dancer rollers control web tension deviations and actuate a corresponding increase or decrease in the breaking force. Tension control on each rewinding shaft is performed by means of independent AC motors. A separate shaft drive makes it possible to do the in-line slitting of the web with chequerwise rolls rewinding.
Pulling cylinder and a rubber coated pressure roller are placed in the upper part of the frame. The pulling cylinder is driven independently by an AC motor synchronized with the main motor. The cylinder has a double-wall structure to allow coolant circulation in order to cool the substrate prior to rewinding.
To facilitate the handling of plastic films and remove static electricity, there are carbon brushes installed on the unwind/rewind unit and before each printing unit.
Hoisting and Drying System
A highly-efficient tunnel-dryer for the final ink drying is mounted at the upper part of the connecting bridge of the press.
There are steel beams mounted on both sides of the bridge to guide electric hoists for loading and unloading rolls of material and plate or anilox cylinders.
In the bottom part of the connecting bridge before printing units there is an automatic web guiding system with steering guides.
Digital Press Control System
The press is equipped with a digital control system with programmable logic controller (PLC). All main control functions are performed via the main control panel with a color touch-screen display.
Setting and displaying of current working parameters is carried out via touch-screen display. All information is displayed in the English language.
The control panel is used to actuate the following functions:
- start/stop of the entire press or its separate units;
- selection of working modes;
- adjustment of press operation speed;
- setting a dryer's temperature and air velocity;
- switching on/off of color stations;
- switching on/off of unwind/rewind shafts;
The display shows the following indicators of press performance:
- web speed;
- meter/job counter;
- self-diagnostics system messages;
- operator prompts.
Characteristics of Idyllic FP presses
Number of Color Stations |
4, 6, 8, 10 |
Max. Operation Speed |
300 m/min |
Web Width |
700 - 2100 mm |
Repeat Range |
300 - 1200 mm |
Max. Unwind/Rewind Diameter |
1300 mm |
Tension Range |
2 - 50 kg |
Register Accuracy |
± 0,1 mm |
Side and Bottom Frame Thickness |
80-120 mm |
Layout of CI flexopress Idyllic FP 6
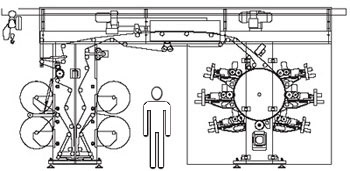
|