Central impression cylinder with direct drive
Idyllic FPA uses highly reliable electronic components of the leading world suppliers
Connecting bridge with powerful hot air dryers
Fully automatic printing units of Idyllic FPA allow for very quick change of jobs
Idyllic FPA 8-850 press performs printing at speed 500 m/min.
|
Highly automated central impression drum flexographic printing presses:
Idyllic FPA wide web flexographic printing presses are an innovative development from the Idyllic team. Above all, these presses distinguish themselves by their high degree of automation. Idyllic FPA presses are equipped with automatic pressure and registration systems, sleeves system, and non-stop rewinding and unwinding systems. These flexopresses have an self-diagnostics system, modem remote service control system, Idyllic FPA stores all printing parameters in its memory, making it possible to repeat already printed runs, etc.
Using all the latest developments in the flexographic industry, the Idyllic team has achieved an outstanding level of productivity, reliability and effectiveness in Idyllic FPA. The design perfection and automation of Idyllic FPA presses make it possible to print the most difficult high lpi jobs. In addition, changeover time on Highly Automated Idyllic FPA presses is minimal. And these are the determining factors in the efficient use of printing equipment.
Idyllic FPA presses can be equipped with wide range of optional equipment. They work with alcohol- and water-based inks, UV-inks, for one- or two-sided and mirror printing.
Presses are intended for printing on flexible packaging materials, such as: plastic films, aluminum and backed foil, BOPP, LDPE, LLDPE, Cast PP, PET, coextruded films, laminated materials, paper, and cardboard. Idyllic FPA presses have a very wide range of substrate thickness starting from 7 microns.
Printing Unit
The printing unit consists of a U-type highly solid frame with solid base made of heavy-duty structural steel. Printing stations are locked in the frame's side-walls.
Chromed double-wall central impression drum with thermostatic control rotates on precision-selected radial-thrust bearings. Idyllic uses central impression drums of German origin, manufactured by Drink&Schloessers Company - the main supplier of central impression drums for flexography in the world. The highest manufacturing quality at factories in Germany renders it possible to achieve minimal, up to 10 mcm, of total cylinder radial beat, to decrease surface roughness up to 23 mcm and to apply chrome protection coating, over 150 mcm, on a drum surface.
Idyllic flexopresses are available both - gear-driven and gearless. Even in gear-driven presses the design makes it possible to avoid all the problems typically associated with all gear-driven presses. The press is driven by a special system. AC servomotor with integrated reducer is positioned on the outer surface of the printing unit's side frame. The motor drives the central impression drum by its shaft directly. Rotation is transferred to color stations via a bull gear positioned at the end of the shaft of the CI drum. The bull gear has a synchronization function, not a power function.
For easy maintenance of the press a supplementary set of ladders is supplied.
Color station of new generation design
The color station is equipped with highly efficient chambered doctor blade systems. Doctor blade change is simple and does not require chamber disassembly. High-performance interstation hot-air dryers are installed after each printing station.
Solid hard, plate, and ceramic anilox sleeves are used in the color stations. Sleeves disengagement is automated and is carried out with the help of special trolleys to allow for quick change of jobs.
During machine stoppage, rollers of color stations are automatically disengaged in accordance with a special algorithm, providing for the self-cleaning of the plates. Anilox sleeves continue to rotate, driven by separate electric motors in order to prevent ink from drying.
Register and printing pressure adjustment systems are automated and are managed from the central control panel. The press features a memory function to store parameters of previously printed jobs, which allows for the quick repetition of jobs with their previous settings. This reduces downtime between jobs greatly. All the printer needs to do when changing the job - is to place new plate sleeves and to load all the job's parameters from the central control panel by pressing only a few buttons. Idyllic FPA does all the rest: it will set up pressure, register, dryer temperature, and other parameters.
The video-inspection system with motorized movement is located immediately after the last printing station, allowing for more effective monitoring of image register fluctuation.
High stability of color alignment on Idyllic FPA presses - is a guarantee of perfect printing quality.
Precision of image alignment of the whole run on Idyllic FPA presses is 0,1mm even with substantial alteration of printing speed during speeding and braking. It is provided by:
- original supporting of main gear of the CI-drum inside the frame, allowing to have short roller journals;
- thick solid walls mounted on heavy solid base;
- stiffness of structure and precision of mechanism operation;
- high precision of components manufacture and assembly of units;
- system of inking system secure fixation during printing mode;
- original construction of registration system, beating and skewing of bearings.
Unwinding and Rewinding Units
The unwinding and rewinding units represent a robust structure with monolithic steel walls. Units are positioned symmetrically on both sides of the frame. There is also housed the temperature-controlled pulling roller with rubber coated pressure roller and dancer rollers. The pulling roller is driven by an AC motor independently, synchronized with the main motor. Synchronized motor rotation ensures steady web tension in the printing area.
There are two air shafts mounted symmetrically on both sides of the frame, to mount reels. To maintain constant web tension at the unwind, both shafts are equipped with electromagnetic powder brakes. An independent digitally controlled asynchronous AC motor ensures consistent web tension on rewind.
To facilitate the handling of plastic films and remove static electricity, there are carbon brushes installed on the unwind and rewind units and before each color station. The unwind unit can be equipped with a corona treatment unit for films. To avoid material wreck at the rewind, the rewind unit features a banana roll and a web guiding system.
Connecting Bridge
The bridge connects the printing unit with the unwind and rewind units. A tunnel dryer is mounted on the upper part of the connecting bridge. Air is heated by means of tubular electric heaters and the supply fan supplies the air. At machine stoppage, hot air supply is automatically discontinued by means of the air control valve. The connection bridge also houses the supply fan and tubular electric heaters of the interstation dryers.
The press features a web threading system making it possible to work with complex substrates. Pulling rollers are parallel by design. At that, it is possible to adjust all rollers separately.
An automatic web guiding system with sliding guides can be installed in the bottom part of the connecting bridge before the first printing station. There are steel beams mounted on both sides of the bridge to guide the electric chain hoists. Hoists are used for loading and unloading reels of material.
Digital Press Control System
The press is equipped with a digital control system with programmable logic controller (PLC). All main control functions are performed via the main control panel. Setting and displaying of current working parameters is carried out via color touch-screen display. All information is displayed in the English language.
The press features a remote service control system. The system facilitates remote Internet or phone modem connection with the Idyllic service center for remote diagnostics and even elimination of problems on the press located at the customer's site. The press features self-diagnostics and operator error-proof systems.
The control panel is used to actuate the following functions:
- start/stop of the entire press or its separate units;
- selection of working modes;
- selecting/storing a job's settings;
- adjustment of press operation speed;
- setting a dryer's temperature and air velocity;
- switching on/off of color stations;
- switching on/off of unwind/rewind shafts;
- printing pressure and ink transfer adjustment;
- register adjustment of color stations;
The display shows the following indicators of press performance:
- web speed in the print mode;
- meter/job counter;
- self-diagnostics system messages;
- operator prompts.
Characteristics of Idyllic FPA presses
Number of Color Stations |
4, 6, 8, 10 |
Max. Operation Speed |
500 m/min |
Web Width |
700 - 2100 mm |
Repeat Range |
300 - 1220 mm |
Max. Unwind/Rewind Diameter |
1500 mm |
Tension Range |
2 - 125 kg |
Register Accuracy |
± 0,1 mm |
Layout of highly automated CI flexo press Idyllic FPA 8
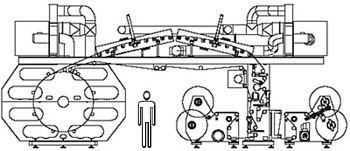 |